Forming Technology
Forming Technology
Gob shape Optimization
Gob is a piece of hot glass which is pushed out from a melting furnace and cut with the specific weight. Gob shape is influenced by glass temperature, pressure at which glass is pushed out from a furnace and a cutting speed. There is an optimal gob shape for each glass container, which enables the most stable forming. We save images of such an optimal gob shape of every product in a computer and use the saved images for checking if a gob is cut in the optimal shape in order to replicate the stable forming.


Bottle Surface Treatment
Resin Coating (TMC®:Toyo Multi Coat)
TMC (Toyo Multi Coat) is a resin coating which enables the use of ultra lightweight glass containers for returnable bottles. This coating is made of urethane resin and the layer thickness is about 30μm. TMC has a resistance to alkali and scratching. The TMC coated ultra lightweight bottle (900ml, 260g) can maintain the initial strength after being used and collected.
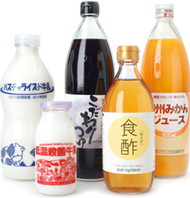
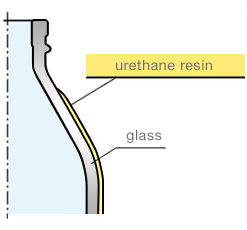
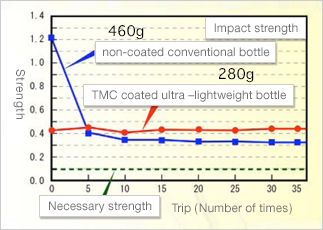
Finish Strengthening by Surfaace Treatment
The technology for increasing the impact strength of bottle finish by silica coating has been developed. The coating layer with the thickness of 50 to 700nm, which is consisted of many-layered silica chemical compounds act as a cushioning material to mitigate shock results in increase of the bottle finish strength.
The glass bottle finish has the potential to break by a small impact caused by bottle falling. This silica coating is expected to reduce such potential of breakage and Toyo Glass is promoting the research and development for practical applications.
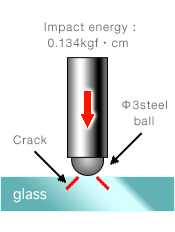
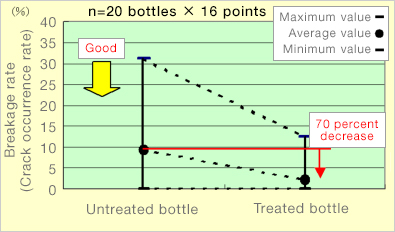
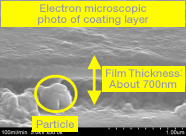
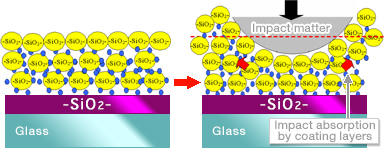
Analysis of Defect-Causing Factor・Countermeasures
Interference simulation between glass and mold
Glass containers are formed by open-close movement of a set of split molds. If the mold interferes with glass during the movement, it may cause a crack on glass surface. Toyo Glass simulates the variation of such interference conditions depending on a mold shape in order to prevent the defect from occurring.
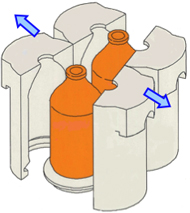
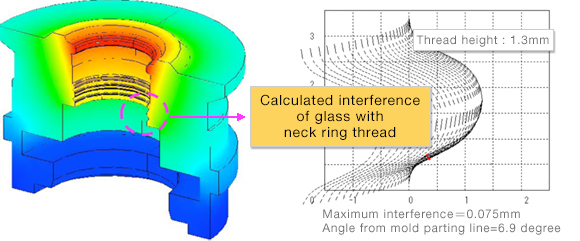
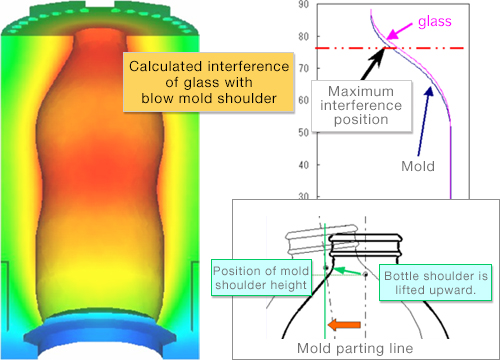
Defect occurrence prevention simulation in blow process
A parison is blown by high-pressure air. Defects tend to occur during this blowing process depending on how a parison swells. When the middle area of parison body swells late, glass around this area cannot be completely contacted with the mold. To prevent this problem, Toyo Glass has improved the mold cooling method to eliminate the delay in parison body swelling. This is a successful example that a problem in the blowing process was found by simulation and was solved, as the result, we could prevent this defect from occurring.
This is a situation where a defect happens easily.
Countermeasure: Change of the mold shoulder cooling condition.
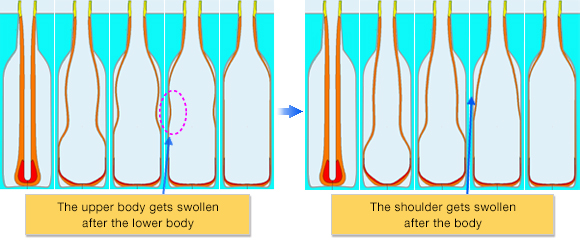