Inspection Technology
Inspection Technology
Rejection of Foreign Particles and Blisters
Gob Image Analysis
As glass containers are formed into complex shapes, it is difficult to detect minor defects which may lower product qualities. So, we, Toyo Glass, have been studying how to detect preliminary causes which result in defects of a glass container after forming, at a stage when glass is in a cylindrically-shaped gob state. In the past few years, we have developed a technology to detect foreign particles and blisters in a gob by taking images of a gob which emits lights at high temperatures using a line sensor camera. It is possible to manufacture high-quality glass containers by detecting defects when a glass container is at the gob stage before being formed.
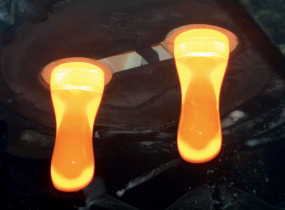
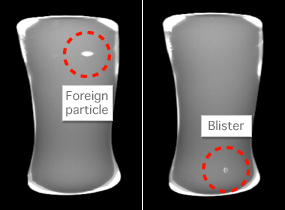
Rejection of Defective Glass Containers
Detection by Highly Sensitive Cameras
In order to improve glass container qualities, Toyo Glass has been developing non-contact automatic inspection devices which inspect the shape and poor appearance of a glass container with the latest and image processing technologies, analyzing the characteristics of glass. Recently, we have developed a technology which detects multiple defects such as foreign particles, blisters and poor bottle shapes, by measuring the shape of the finish, the body and the heel of a bottle, with a line sensor camera and an area sensor camera. Also, Toyo glass is working on developing another type of inspection device to inspect poor appearance by recognizing the patterns of a glass container.
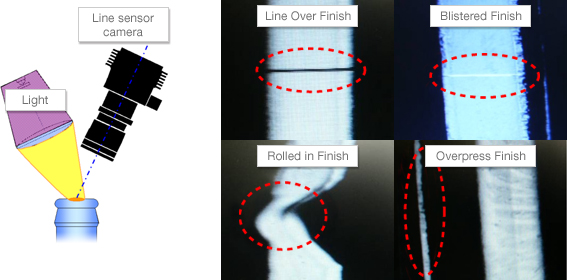
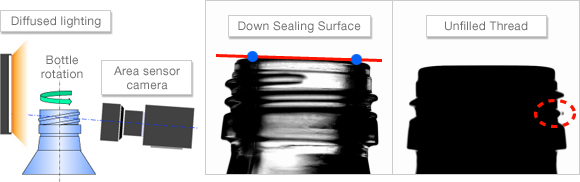
Quality Control Network
For quality control, Toyo Glass conducts online measurement of dimensions and mass of each part of a glass container, and also automatic product strength tests. In addition, we inspect and detect more than 20 different defects and abnormal values with the integrated inspection machines, each containing the inspection devices which have been uniquely developed by Toyo Glass. By connecting these machines and devices in a network, it is possible to collect data in real time for the production processes, from forming to inspection. This data aggregation enables us to promptly perceive any abnormality in the production process and to implement quick reactions to correct the problem.
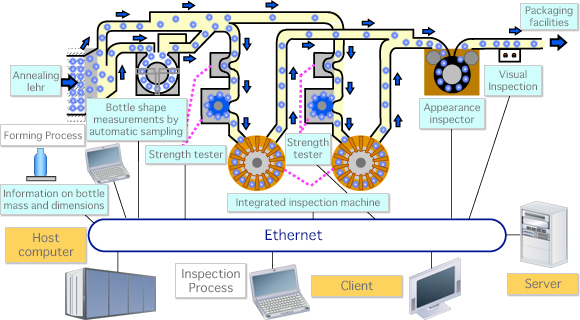