Design Technology
Design Technology
Bottle Shape Design
A glass container has a fewer limitation of shape design than other material containers and it is possible to design a variety of bottle shapes. However, lightweighting increases the degree of difficulty in forming a glass container and decreases a mechanical strength of glass container. In order to predict and evaluate in advance a bottle shape with superior formability and enough mechanical strength taking advantage of the flexible shape design, computer simulation analysis is important.
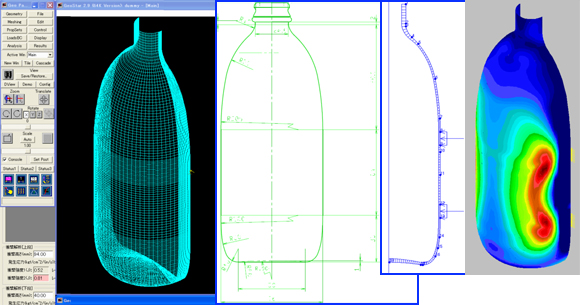
Optimal Parison Design
Temperature calculation during glass bottle forming
A gob (a piece of hot glass) of 1,150 ℃ to 1,200 ℃ is formed into a parison after it is loaded into a blank mold. The parison is transferred to a blow mold and blown by compressed air results in forming of a glass bottle. The proper forming conditions to produce quality glass containers are found by calculating temperature transition in this process.
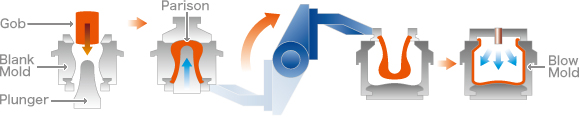
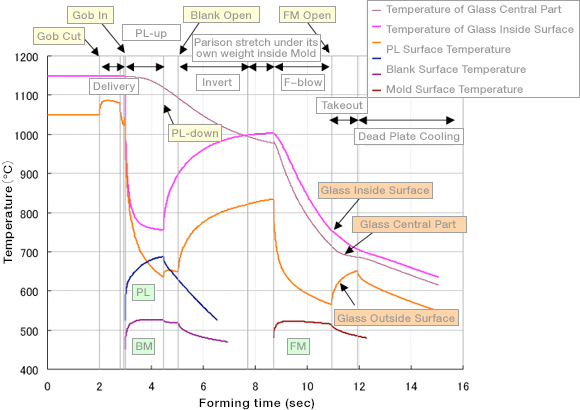
Simulation of Glass Distribution
Thickness distribution of a glass container mainly depends on a parison shape and glass temperature. In order to reduce glass thickness to the limit, it is necessary to simulate an overall bottle thickness at the design stage. Such thickness simulation finds an optimal parison shape and forming conditions for a glass container.
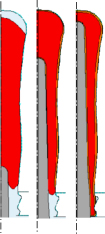
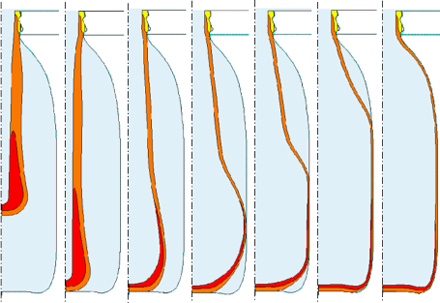
Bottle Strength Analysis
In recent years, the technology to produce a glass container with ultimate thinness is established and such glass containers have been shipped to market. Lightweighting a glass container makes bottle thickness thin, and as a result, a mechanical strength of glass container is reduced. Glass containers are delivered to consumers through various distribution channels. Strength analysis is necessary to prevent any problem regarding bottle strength during filling process and transportation. Appropriate glass thickness and bottle shape are determined by a strength analysis result and a secure and safe container is manufactured.
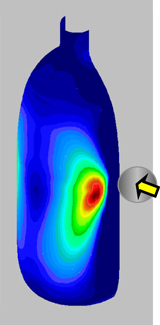
strength analysis
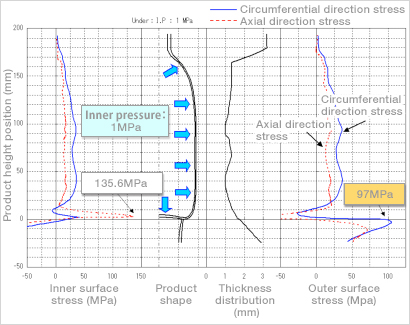
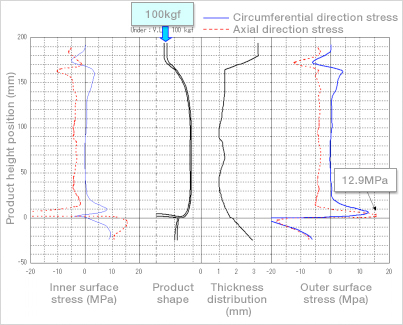
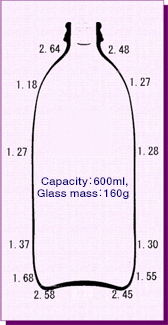